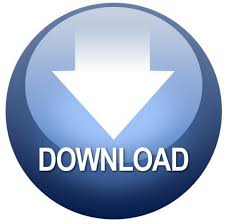
ĭepending on the layer configurations at the microscale, a different mechanical response is expected at the macroscale. For a successful characterization of FDM materials by the FEM, material models are sought after in order to represent characteristics of FDM accurately. Finite element method (FEM) is the standard approach in solid bodies for computing structural response under mechanical loading. Since additive manufacturing is using a layer-by-layer technique, there is an added inner structure related material response. įor the computation of deformation in a structure, we need to model the material's response by means of a constitutive equation, also called the material model. In those fields, mechanical response must be predicted in the design phase.

Design freedom makes FDM adequate for industries, where complex parts are needed among others in aerospace, biomedical automotive, aeronautics, biomechanical as well as research especially for studying metamaterials. In polymer Fused Deposition Modeling (FDM), the layered fabrication process enables increased design freedom. Among them, Fused Deposition Modeling (FDM) technique has been developed in the 1980s, and it is seen as a new candidate next to the conventional manufacturing methods such as turning, grinding, milling, casting, etc. There are different additive manufacturing methods such as: Stereolithography (SLA), Selective Laser Melting (SLM), Binder Jetting, Direct Energy Deposition, Kinetic Fusion, Laminate Object Modeling (LOM), etc. They represent a new trend for prototyping as well as they may augment or even partly replace conventional manufacturing methods. Graphical AbstractĪdditive manufacturing methods are frequently and increasingly employed manufacturing techniques of the 21st century. We found out that the layer thickness and overlap ratio parameters significantly alter the microstructures and thereby, stiffness of the macroscale properties. In this regard, a systematic methodology is presented for acquiring the anisotropy from the process related inner substructure (microscale) to the material response at the homogenized length scale (macroscale). These simulations are validated by experimental characterizations. We use computational homogenization approach for obtaining the effective properties of the FDM-related anisotropic structure. A digital twin of mechanical laboratory tests are realized by the FEM. By incorporating these characteristics, we draw CAD images.
#Tutorial on making a void pantograph code
We develop 2D-digital-image-correlation code with machine learning algorithm, namely K-means cluster, to analyze microstructures (contact surfaces, the changes in fiber shapes) and calculate porosity. Mechanical and optical characterizations are carried out. In order to investigate these process-related characteristics and tailored properties of FDM structures, we prepare FDM-printed poly(ethylene terephthalate) glycol (PETG) samples with different process parameters. Even in use of amorphous materials, FDM creates anisotropic structures effected by the chosen manufacturing parameters.
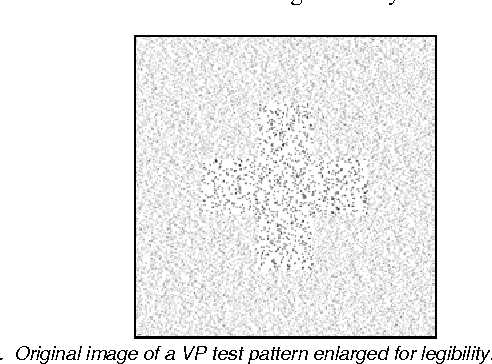

Ample studies are being undertaken for modeling the mechanical characteristics of FDM by using the Finite Element Method (FEM). Additive manufacturing develops rapidly, especially, fused deposition modeling (FDM) is one of the economical methods with moderate tolerances and high design flexibility.
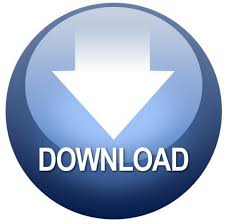